
In modern industry, efficient processing equipment is the key to the competitiveness of enterprises. As one of the indispensable secret weapons behind industrial innovation, the automatic knife grinder is gradually becoming the preferred equipment for many enterprises.
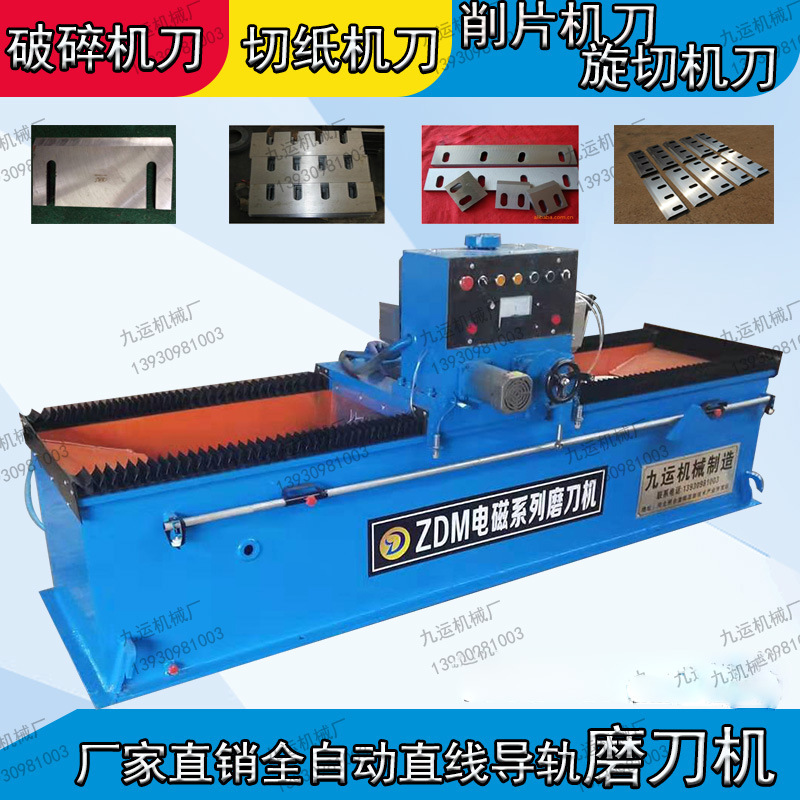
The core value of the automatic sharpener is not only its high precision and durability, but also its ability to significantly reduce the time cost of manual intervention. The fuselage design made of carbon steel and built through the gantry structure makes the overall operation more stable and has a long service life. The aviation turbine reduction system cooperates with the rack and round-trip transmission, which further enhances the smooth performance during the stroke drive.
In addition to traditional rotary cutting machinery, this type of equipment is now widely used in many industries, such as plastic pellet manufacturing, paper industry and wood deep processing. Whether you need to handle hard materials or flexible fiber products, can easily deal.
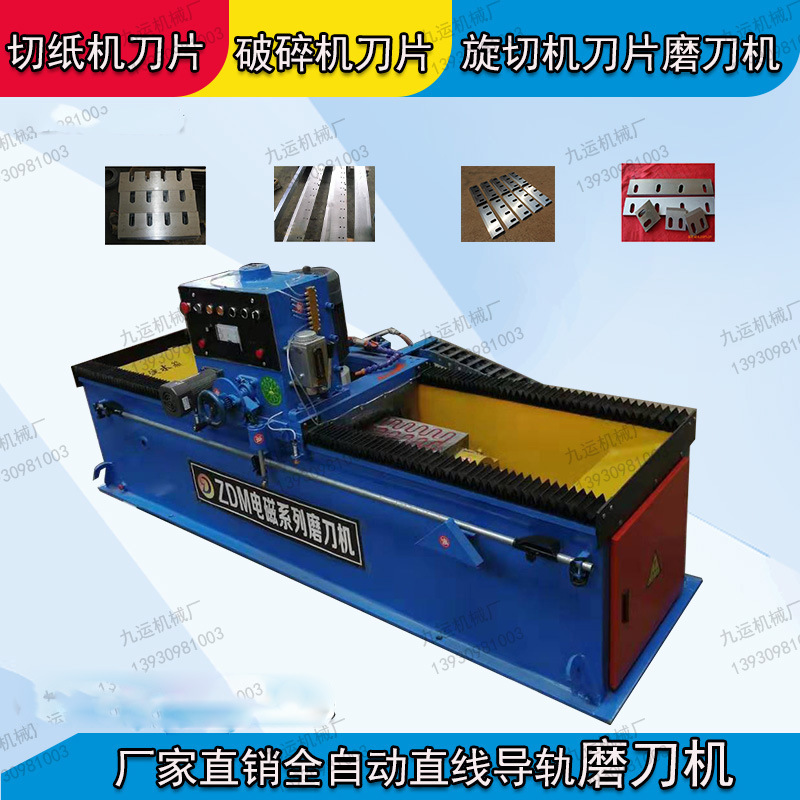
With the continuous development and progress of science and technology, the concept of "electromagnetic" has also been introduced into the new model products. Compared with the previous way of relying solely on physical friction to complete the task, the new addition of this function can not only achieve higher efficiency of cutting edge trimming work, but also greatly reduce the probability of various problems caused by overheating.
At the same time, many improvements have been made in terms of human considerations-for example, fully automated devices greatly simplify the operation process; intuitive and friendly interface allows even first-time users to quickly master basic skills requirements, and so on. The optimization of these details undoubtedly brings more convenient practical experience effect for the enterprise.
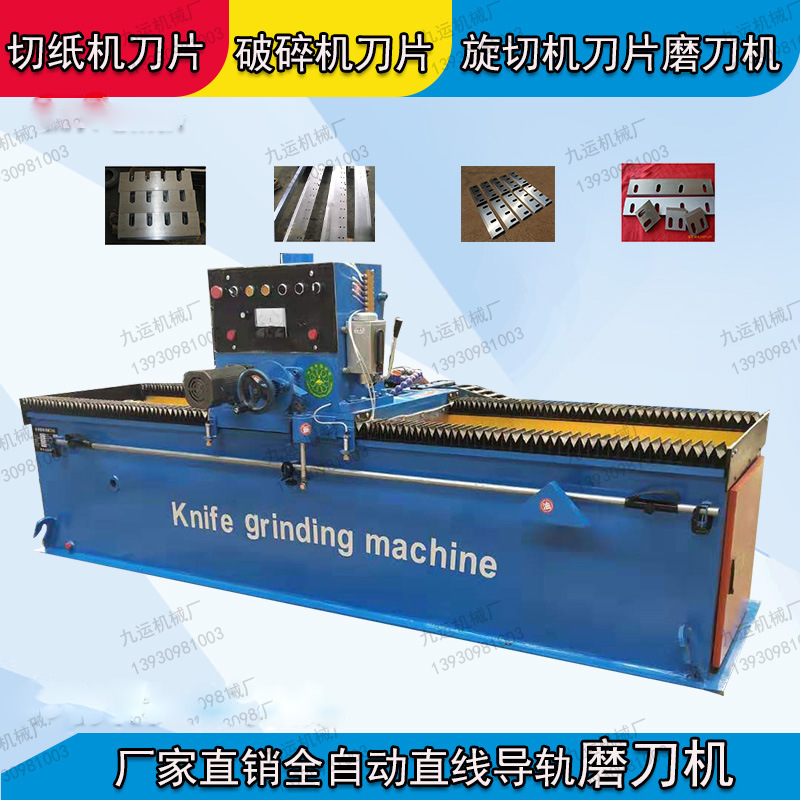
However, with excellent performance, it is still difficult to maintain good condition for a long time without proper maintenance methods. Therefore, it is recommended that users regularly check the wear of key components and replace damaged parts in time. In addition, it is necessary to pay attention to the knowledge accumulation of lubricant selection and dosage control, so as to give full play to the maximum potential of this system in a real sense.
How to make a wise decision in the face of a wide variety of brands and models on the market? It is a very important step to first identify your specific needs. Next, you can screen and compare by consulting relevant evaluation materials or consulting professional opinions, and finally determine the best option to meet the conditions.
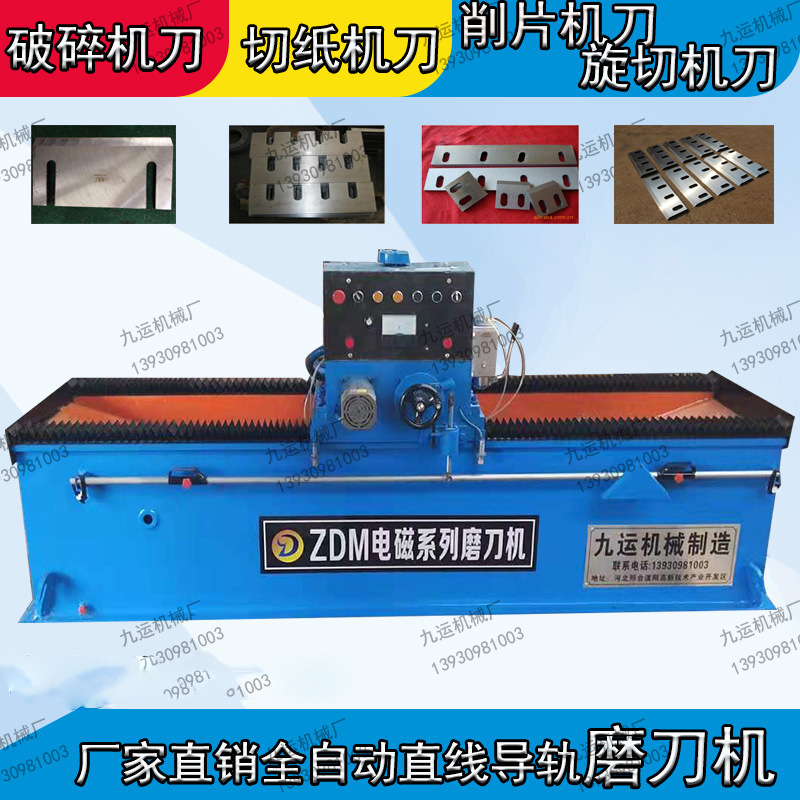
in order to better prove the authenticity of the above point of view, a successful case is listed here for reference: the ordinary manual machine originally used by a large packaging factory can only complete about 50 tool repair tasks every day and often lead to high rework rate due to large errors. Since the introduction of a new generation of fully automatic version, not only the work efficiency has increased by more than three times, but also the quality of the finished product has been significantly improved.
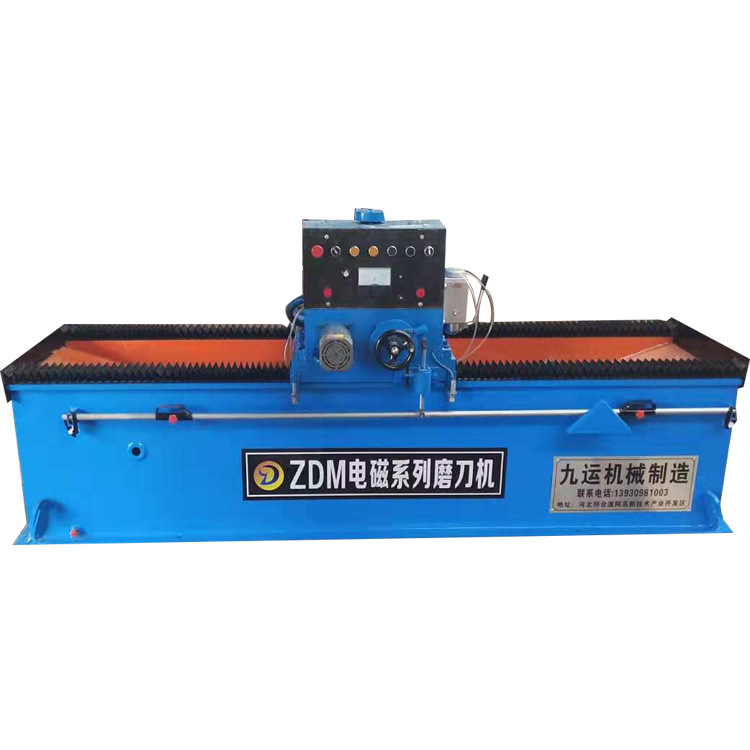
In short, choosing a professional solution that suits your business model and development direction is the way to win. I hope this article can help more business owners who are looking for ideal partners to find the right artifact!
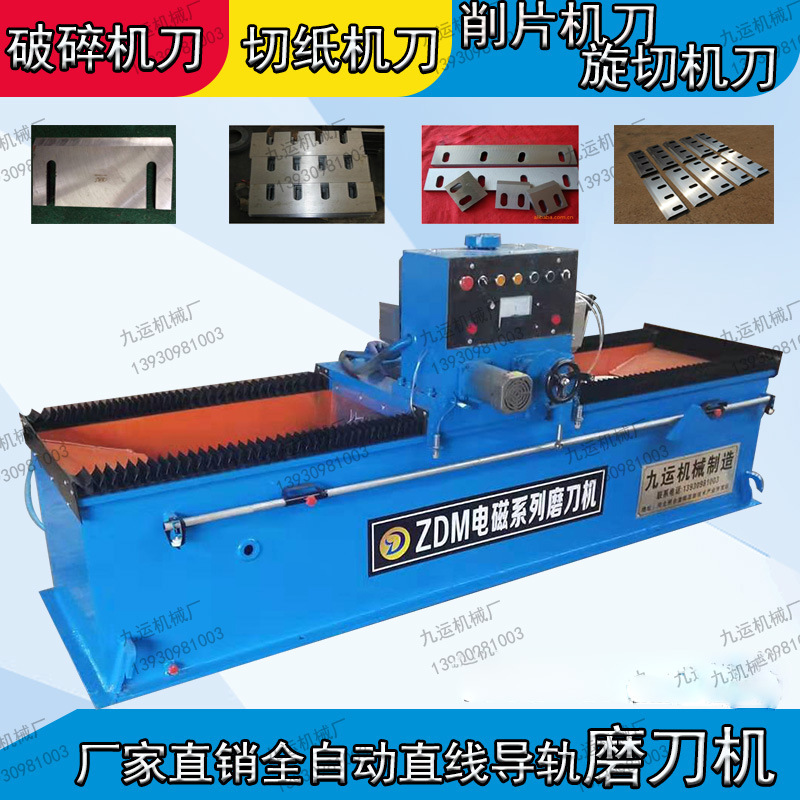