
With the advancement of industrial technology, the traditional manual sharpening method has gradually been replaced by more efficient automation equipment. Today, automatic sharpeners have become an indispensable part of many industries, especially for companies that need frequent replacement and trimming of tools.
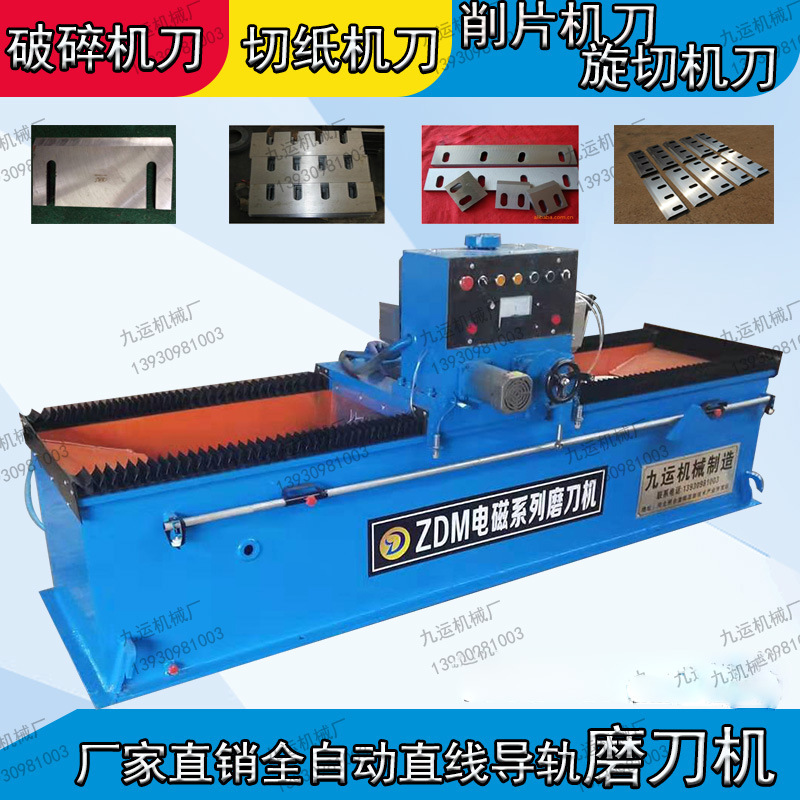
Our fully automatic knife grinder not only inherits the advantages of traditional equipment, but also has been comprehensively upgraded on this basis. The machine is made of carbon steel material, and combined with the gantry body design, so that the whole equipment has higher stability and durability. In addition, the addition of the aviation turbine deceleration system further improves the smooth performance during operation.
Electromagnetic drive is one of the core highlights of this machine. Compared with ordinary motor drive mode, it has faster speed response ability and more precise operation accuracy. This means that users can easily complete a variety of complex grinding tasks without worrying about errors or damage to the surface of the workpiece.
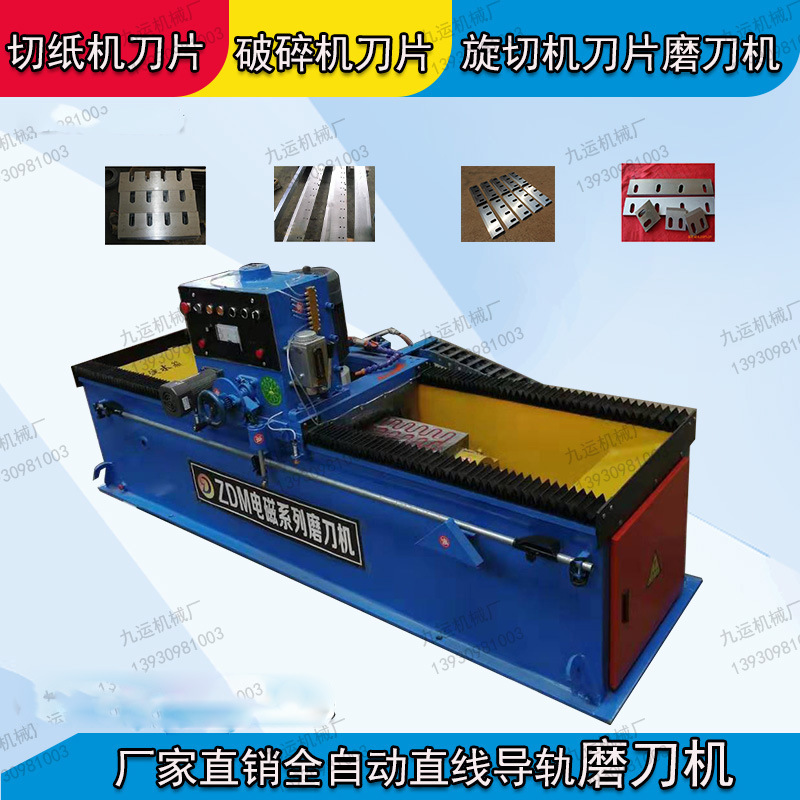
In addition to the powerful hardware configuration, this product can be widely used in many fields. For example, the cutting process in the printing industry requires the use of sharp and evenly distributed edge shape of the metal sheet; wood processing process also requires regular maintenance and repair of circular saw discs, and so on. In short, as long as there is any need for blade maintenance, we can consider introducing such an all-round player to help solve the problem.
a technical director from a large packaging factory once shared his experience: "since the introduction of this system, our workshop can save nearly two hours a day of time originally spent on manual adjustment. And the quality of the finished product has also been significantly improved, and the customer feedback is very satisfied. "
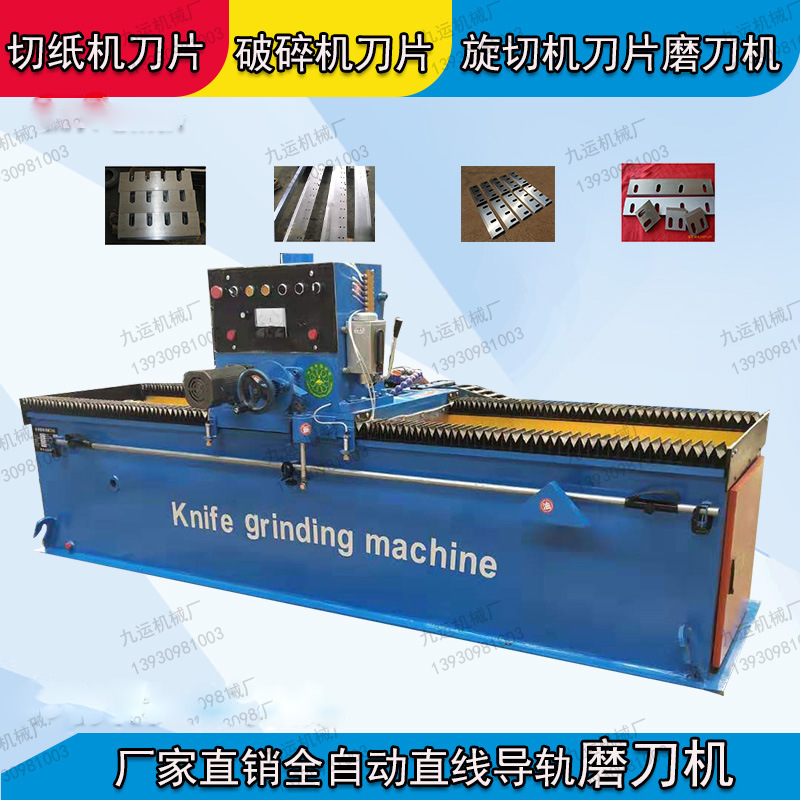
If you are looking for a professional-grade automatic sharpening solution for your factory, then the following content will be very important. First, make clear what kind of material you are mainly facing (such as cemented carbide or stainless steel) and then pay attention to the following key indicators:
- Maximum processing width: Determine whether it can cover the range of all objects to be processed.
- Minimum adjustment step distance: Ensure that fine adjustments reach the ideal state.
- Safety precautions: Protect operators from the risk of accidental injury.
Finally, don't forget to verify whether the after-sales service terms provided by the manufacturer are comprehensive and reliable enough! After all, good after-sales support can often save us a lot of trouble at critical moments ~
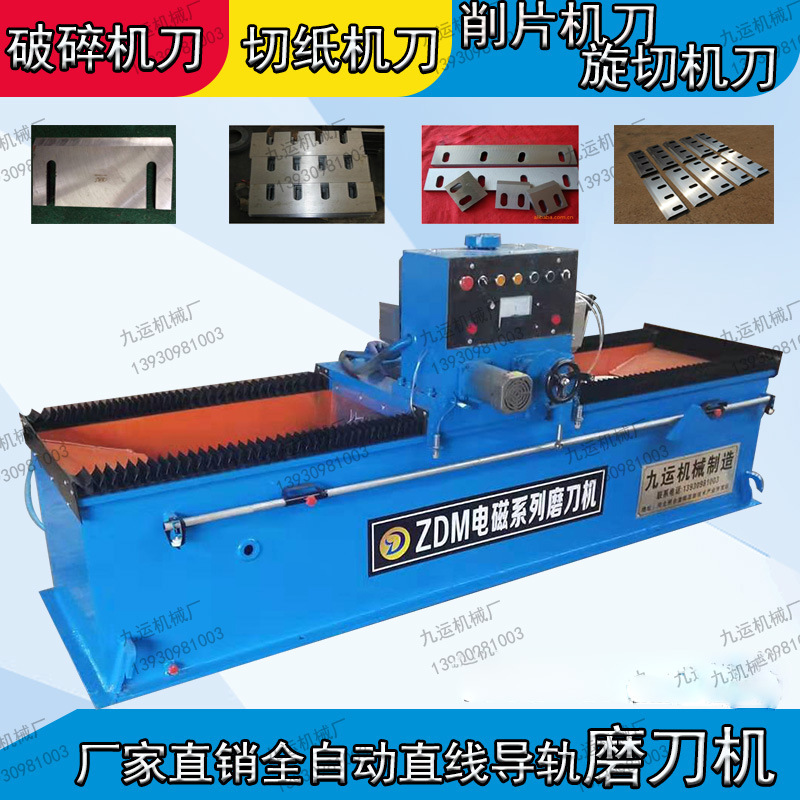