
In modern industry, the manual sharpening method has long been unable to meet the needs of high precision and high efficiency. Traditional manual operation is not only time-consuming and laborious, but also easily leads to error accumulation, which affects product quality. Especially in industries that require frequent tool replacement, this problem is even more prominent.
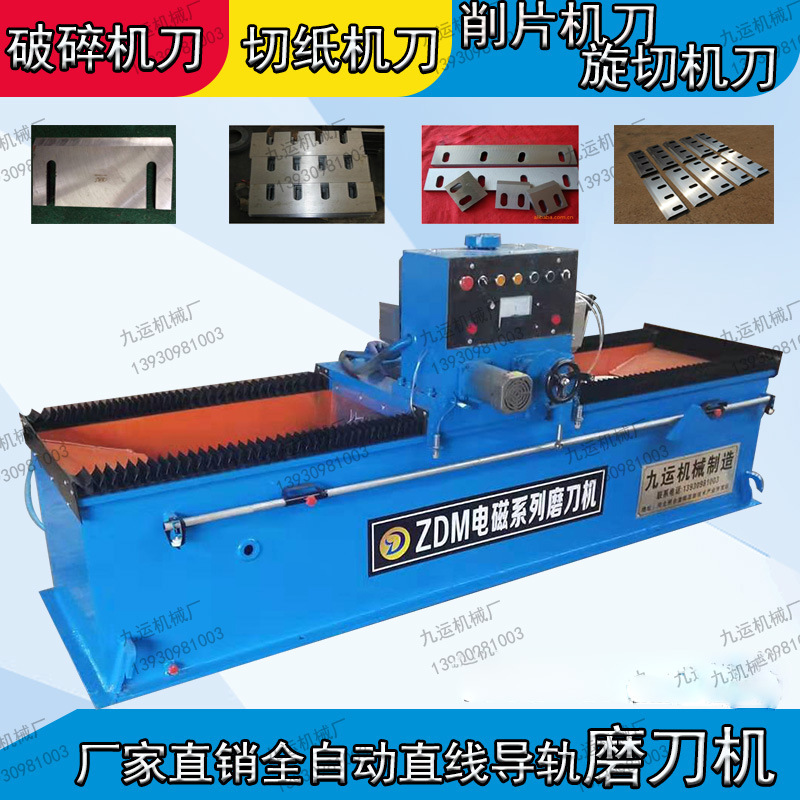
To solve this problem, Xingtai Jiuyun Machinery Factory has launched a new generation of high-efficiency automatic knife sharpeners. Designed for a variety of cutting tools, it can easily handle complex tasks such as plastic pellet processing, blade repair and paper cutting processes.
The core of the equipment is the use of advanced automation technology and sophisticated aviation turbine deceleration system, combined with a gantry-type fuselage structure and a guide rail processed by fine scraping technology to ensure that the entire machine has extremely high stability and long service life.
In addition, the stroke drive part achieves smooth operation through the reciprocating motion of the gear to ensure that each grinding reaches the expected standard. This innovative design allows users to significantly increase productivity while also reducing maintenance costs.
This efficient automatic knife sharpener can meet the challenges in many fields, including but not limited to:
- Printing industry: Used for blade adjustment of paper cutting machine;
- Wood processing industry: For woodworking rotary saws and other similar devices;
- sheet metal industry: responsible for steel plate stamping die maintenance, etc.
Not only that, it can also complete the linear blade trimming work required in the fields of fiber, rubber and textiles.
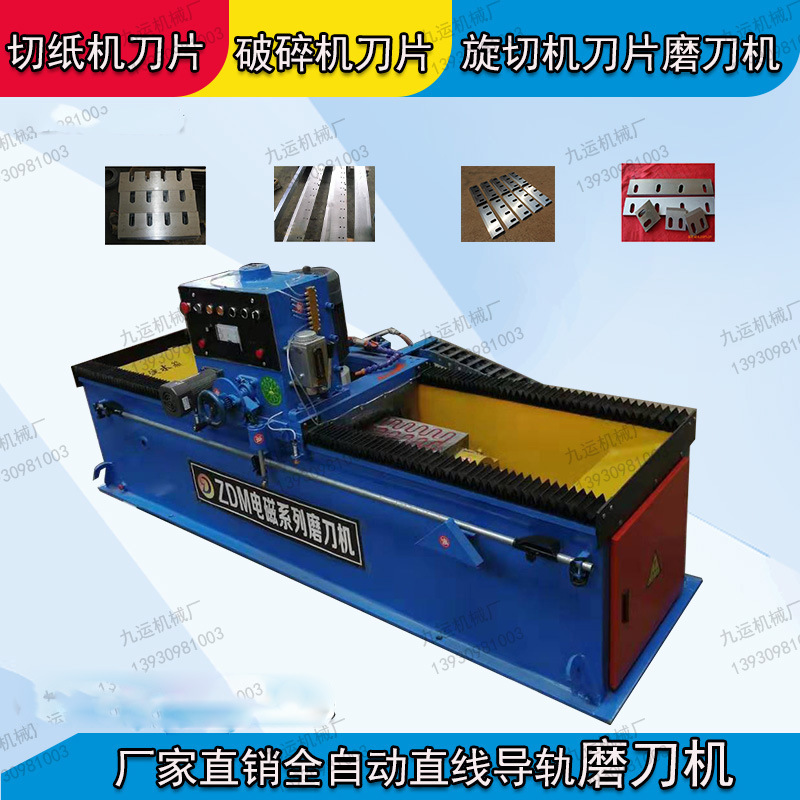
Compared with ordinary manual or semi-automatic models, our full-featured version has obvious advantages:
- Less human intervention means less possibility of human error;
- Faster speed allows the production line to continue to run without waiting for maintenance;
- Higher precision helps maintain consistent quality in the final product.
Studies have shown that after the introduction of such high-tech equipment, an average of at least three hours of operating time can be saved every day, and the scrap rate in each cycle is reduced by more than 10%. For large-scale production enterprises, this means real income growth of thousands or even tens of thousands of yuan per year.
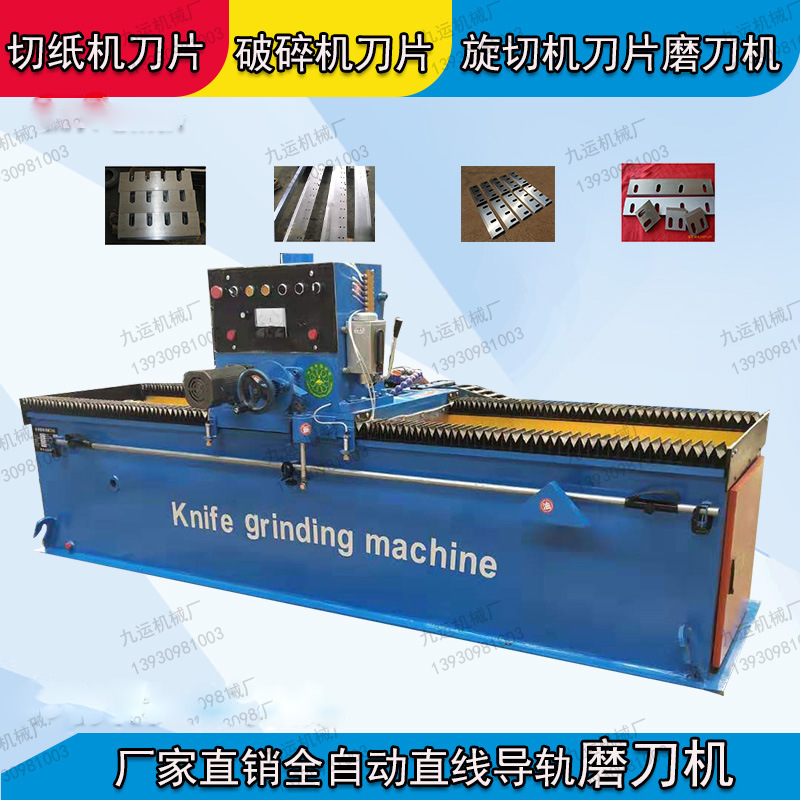
Positive reviews from customers across the country continue to validate the excellence of this product. "Since the installation of this system, the pace of work in our workshop has become much smoother!" A customer in Guangdong said, "I used to worry about downtime due to tool wear, but now I don't have this concern at all." Another Zhejiang business owner added: "It's very cost-effective, and it will be back soon!"
Looking to the future, with the progress of science and technology and the development of technology, intelligent elements will be further integrated into these mechanical equipment. Imagine that when the Internet of Things connection becomes a reality, all parameters can be remotely monitored and adjusted immediately; the artificial intelligence-assisted diagnosis function will find the problem in the first place and warn of potential failure risks in advance...
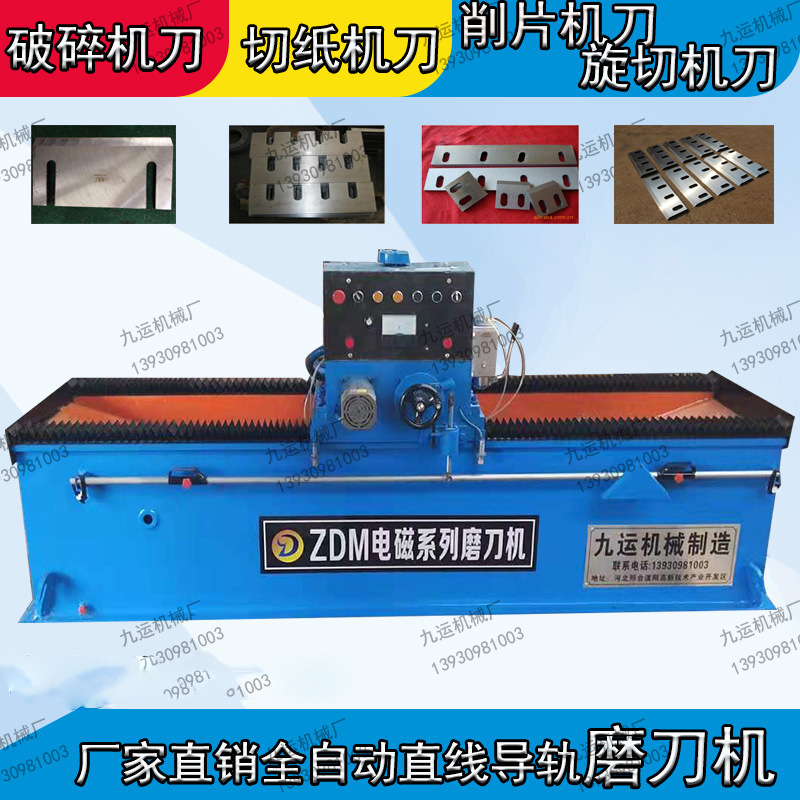
All of this is becoming possible, and you only need to seize the opportunity to be the first to experience the transformative power of the next generation of smart manufacturing.
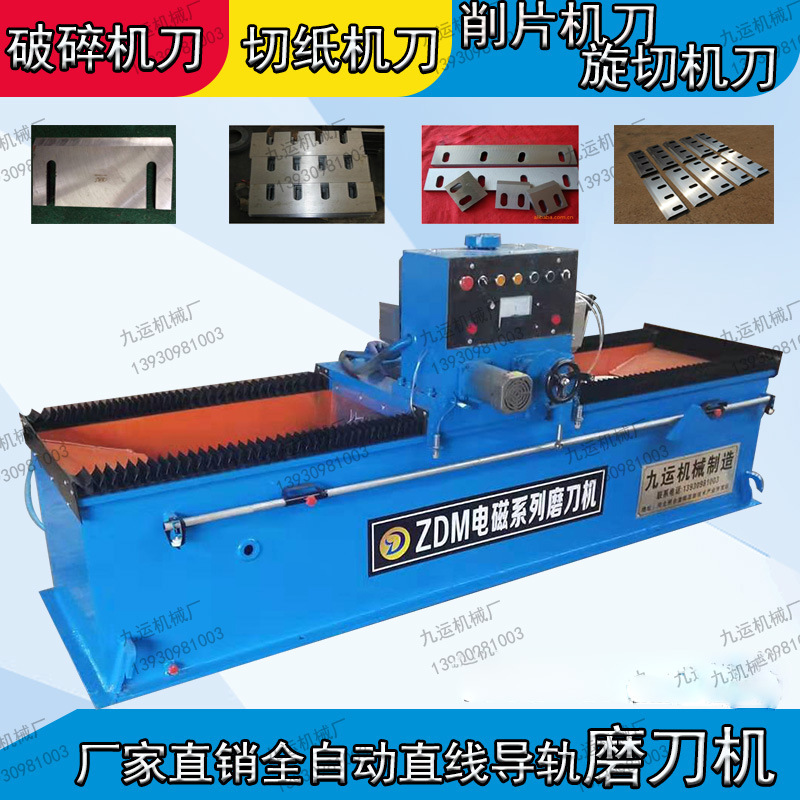