
In modern industry, cutting tools, as an important part of all kinds of machinery and equipment, have a direct impact on product quality and production efficiency. Therefore, regular maintenance of cutting tools has become an indispensable part of the enterprise. However, the traditional manual sharpening method is time-consuming and difficult to ensure consistency, and our automatic sharpening machine can effectively solve this problem.
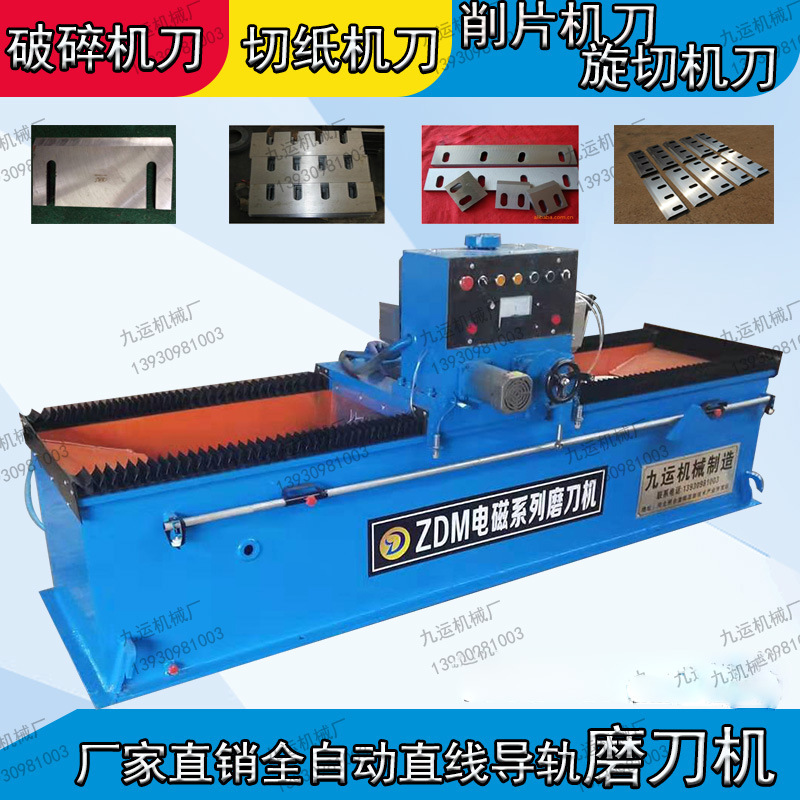
With automation technology and advanced design, this equipment is gradually changing the traditional cutting tool maintenance mode, helping all walks of life to move towards a higher level of productivity.
Automatic sharpeners offer significant advantages over manual operation. First of all, in terms of efficiency, it can work continuously without interruption, which greatly shortens the time required for a single task; secondly, it is the guarantee of accuracy, with the help of highly sensitive sensors and precise control system to complete each step of action adjustment, so as to ensure that every grinding reaches the ideal state.
In addition, this machine adopts a gantry-type fuselage structure with an aviation turbine deceleration system, which always maintains a smooth and smooth operation without jitter, which makes the whole process more reliable and durable.
Electromagnetic technology is one of the core forces behind these capabilities. By using the principle of strong magnetic field to drive the grinding wheel to rotate, it not only improves the power transmission efficiency but also reduces the probability of mechanical wear. Coupled with the finely scraped guide rail surface, the two work together to give the entire device a very long service life while also allowing the quality of the finished product to be fully guaranteed.
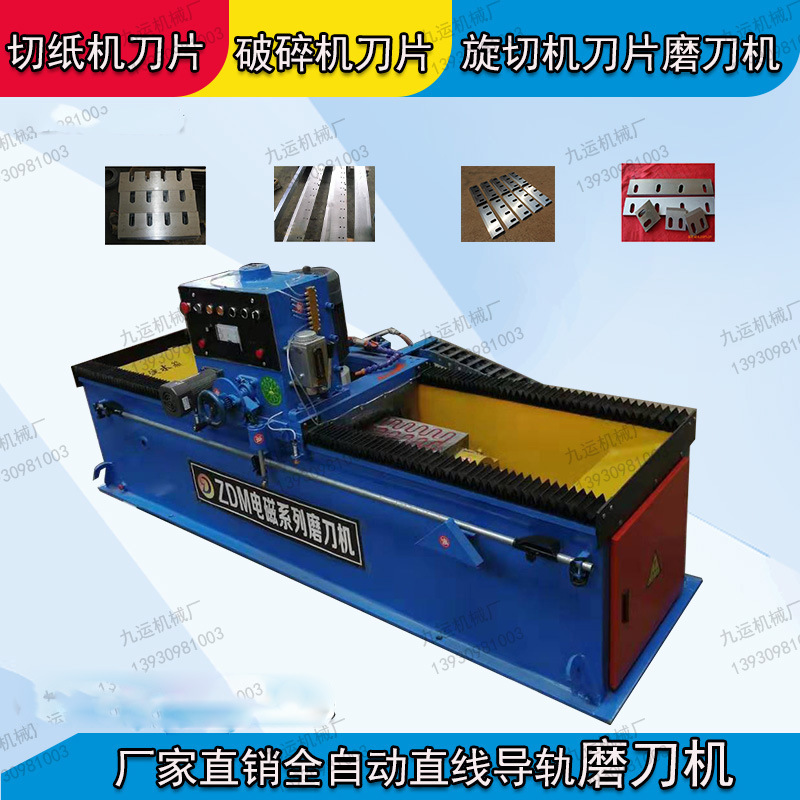
From plastic particle processing to the field of cutting paper to the comprehensive development and utilization of wood and other industries can see its active figure. For example, for the disc-shaped cutting tools frequently used in paper mills, it is easy to meet the requirements of various specifications and sizes by simply setting parameters. However, it is also handy for the steel knives that need to deal with a large number of waste materials recycling projects.
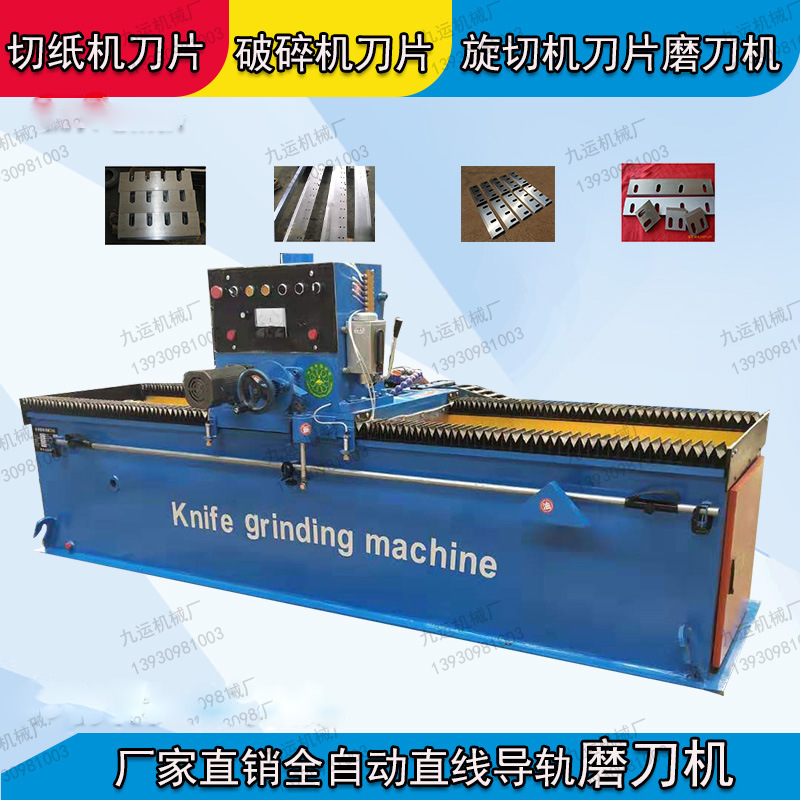
Many of the customers who have already put it into use have expressed satisfaction with its performance. "Since the introduction of this solution, our workshop can save nearly two hours of labor costs every day." The person in charge of a well-known packaging company commented, "And now the edges of all products look more uniform than ever!"
How to make a wise choice in the face of a wide range of similar products on the market? The key is to identify your specific needs and carefully consider the following factors:
- -whether the equipment capacity is sufficient to cover all load levels under the existing scale;
- -Whether the number of types of optional accessories can meet the requirements of special occasions and special circumstances;
- -How to improve the after-sales service system to relieve the problems that may be encountered during later use.
Finally, don't forget that everyday safekeeping is also crucial! It is suggested that the residual water must be thoroughly wiped dry after each cleaning to prevent corrosion. At the same time, the tightness of the screws at each connection part should be checked regularly to avoid the risk of falling off due to vibration, etc.
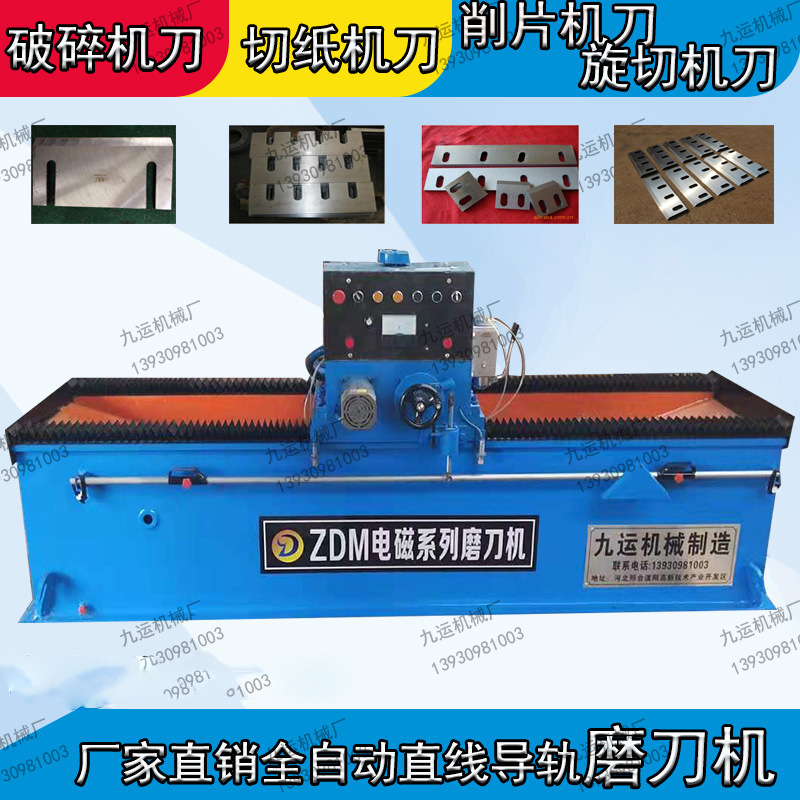